Digital Dentistry Milling vs. 3D Printing Innovations

DESCRIPTION
Explore the latest in digital dentistry: Discover how milling and 3D printing are revolutionizing dental care with precision and innovation.
CATEGORY
3D Printing
CONTRIBUTOR
Antonello Croce
DATE
08/12/23
Introduction to Modern Dental Fabrication Techniques
The field of dental fabrication has undergone a remarkable transformation over the years, evolving from traditional manual methods to highly sophisticated digital techniques. This evolution marks a significant milestone in the journey of dental care, offering precision, efficiency, and customization like never before.
In the early days, dental prostheses were crafted by hand, relying heavily on the skill and experience of dental technicians. While this method had its merits, it was time-consuming and often lacked consistency. The advent of digital dentistry marked a turning point, introducing technologies that revolutionized the way dental prostheses are designed and fabricated.
Computer-Aided Design and Computer-Aided Manufacturing (CAD/CAM) systems emerged as game-changers in the dental industry. These systems allow for the digital design of dental restorations, which are then precisely milled from solid blocks of material using computer-controlled milling machines. The accuracy and speed of CAD/CAM systems significantly improved the quality and efficiency of dental prosthesis fabrication.
More recently, 3D printing technology has begun to make its mark in digital dentistry. This additive manufacturing process builds dental appliances layer by layer, allowing for even more complex and customized designs. 3D printing offers several advantages, including the ability to use a wider range of materials and the potential for faster production times.
This journey from manual craftsmanship to digital precision encapsulates the dynamic nature of dental fabrication. Today, the integration of digital dentistry, CAD/CAM, and 3D printing is not just enhancing dental practice but is also redefining the standards of patient care and satisfaction in the dental world.
Understanding Milling in Dental Prosthesis
Explanation of the Milling Process
Milling in dental prosthesis represents a cornerstone of modern digital dentistry, primarily facilitated by the integration of CAD/CAM technology. This process begins with the digital designing of the dental restoration. Dentists or dental technicians use specialized software to create a precise 3D model of the required prosthesis, such as crowns, bridges, or veneers. The design is then sent to a milling machine, which carves the prosthesis from a solid block of material, typically ceramic, composite, or metal.
The milling machine, guided by the CAD/CAM software, employs a series of drills and burs to subtractively manufacture the dental restoration. This process involves cutting and grinding the material into the final shape of the prosthesis. Advanced milling machines can operate with high precision, ensuring that the dimensions of the prosthetic are accurate to within a fraction of a millimeter.
Advantages of Milling
Precision and Consistency: Milling offers unparalleled precision in dental prosthesis fabrication. The accuracy of CAD/CAM systems ensures that each prosthesis adheres strictly to the specifications of the digital design. This consistency is critical for ensuring that dental restorations fit perfectly, improving both the aesthetic and functional outcomes.
Range of Materials: Milling machines can work with a diverse array of materials, including zirconia, porcelain, pmma and various composites. This versatility allows dental professionals to choose the most suitable material based on the specific requirements of each patient, such as color matching, strength, and wear resistance.
Speed of Production: Compared to traditional methods, milling can significantly reduce the time required to produce dental prostheses. This efficiency benefits both dental practices and patients, as it allows for quicker turnaround times, often enabling same-day dental restorations.
Reduced Labor Intensity: The automation provided by CAD/CAM systems reduces the manual labor involved in prosthesis fabrication. This not only decreases the likelihood of human error but also allows dental technicians to focus on more complex aspects of dental restoration.
Limitations of Milling
Initial Investment Cost: The cost of acquiring and maintaining CAD/CAM systems and milling machines can be substantial. This investment may be a barrier for smaller dental practices or laboratories.
Material Wastage: As milling is a subtractive process, there is an inherent wastage of material. The block of material from which the prosthesis is carved will always result in some leftover material that cannot be used.
Design Limitations: While milling is highly accurate, there are limitations to the complexity of designs it can produce. Intricate features or undercuts can be challenging to mill, potentially limiting the scope of restorations that can be created through this method.
Maintenance and Operational Skill: Operating and maintaining milling equipment requires specific skills and knowledge. Regular maintenance is essential to ensure the longevity and accuracy of the machinery.
In essence, milling in dental prosthesis, enabled by CAD/CAM technology, stands as a significant advancement in digital dentistry. Its precision, efficiency, and versatility in material use have greatly enhanced the quality and accessibility of dental restorations. However, considerations regarding cost, material wastage, design limitations, and operational expertise are essential when evaluating its integration into dental practice.
The Rise of 3D Printing in Dentistry
Detailed Explanation of 3D Printing Technology in Dentistry
3D printing, also known as additive manufacturing, is a revolutionary technology that has made significant inroads in the field of dentistry. Unlike traditional subtractive methods like milling, 3D printing builds objects layer by layer from the bottom up. In the context of dental applications, this technology involves creating dental prostheses, such as crowns, bridges, and dentures, as well as orthodontic devices, directly from digital models.
One of the most prominent forms of 3D printing in dentistry is Stereolithography (SLA). SLA works on the principle of photopolymerization, where a laser cures liquid resin into a hardened plastic. The process starts with a vat of photosensitive liquid resin. A build platform descends into this vat, and a laser, guided by a digital design file, traces the first layer of the prosthesis onto the surface of the resin. Wherever the laser touches, the resin hardens. The platform then moves up, allowing a new layer of resin to cover the surface, and the laser solidifies the next layer. This process repeats, building the dental prosthesis layer by layer.
Advantages and Unique Features of 3D Printing
Complex Geometries and Customization: 3D printing excels in creating complex structures, which can be challenging or impossible to achieve with milling. It allows for intricate designs and fine details, making it ideal for custom-fit dental appliances and prostheses.
Efficient Use of Materials: Since 3D printing is an additive process, it minimizes waste compared to subtractive methods. Material is only used where it is needed, making it a more sustainable choice.
Rapid Prototyping and Production: 3D printing technology enables rapid prototyping, allowing dental professionals to quickly produce models and make necessary adjustments. This accelerates the overall process of developing and finalizing dental restorations.
Wide Range of Materials: Recent advancements have expanded the range of materials available for dental 3D printing, including biocompatible resins. These materials can mimic the properties of natural teeth, offering both aesthetic and functional benefits.
Accessibility and Cost-Effectiveness: With the decreasing cost of 3D printers and materials, this technology has become more accessible to dental practices of all sizes. It allows for in-house production, reducing the reliance on external dental labs and associated costs.
Enhanced Patient Experience: 3D printing can reduce the number of visits and the amount of chair time required for dental restorations, offering a quicker and more comfortable patient experience.
Innovative Applications: Beyond prostheses, 3D printing has innovative applications in dentistry, including the fabrication of surgical guides, orthodontic devices, and educational models, further broadening its utility in the field.
In summary, the adoption of 3D printing, particularly SLA technology, in dentistry marks a significant step forward in the field. Its ability to produce highly customized, complex dental restorations and devices efficiently and sustainably positions it as a key component of modern digital dentistry. As technology continues to advance, its role in dental care is set to expand, further revolutionizing dental treatment and patient care.
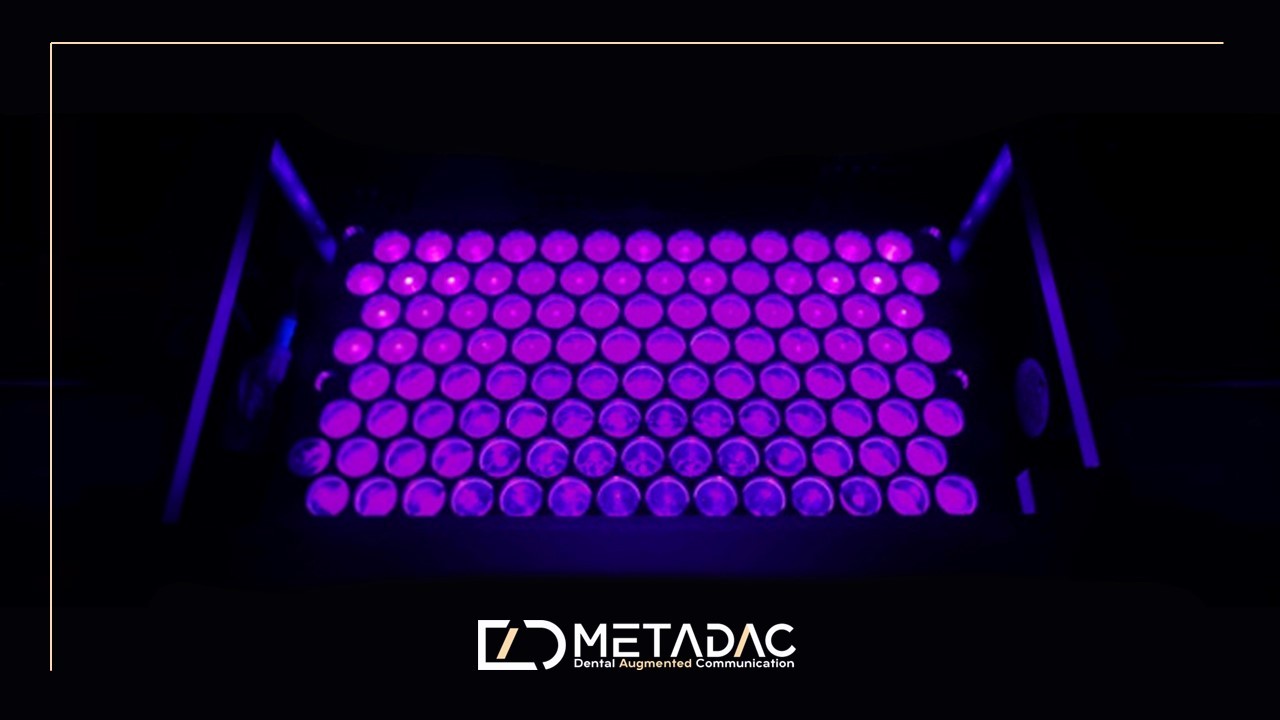
Comparative Analysis: Milling vs. 3D Printing in Dental Fabrication
The advent of digital technology in dentistry has introduced two predominant fabrication methods: milling and 3D printing. Both methods possess unique advantages and limitations, particularly in terms of precision, material usage, cost-effectiveness, and time efficiency. Understanding these differences is crucial for choosing the appropriate method for various dental applications.
Precision
Milling: Known for its high precision, milling is ideal for creating dental restorations with intricate details and tight tolerances. The subtractive nature of milling allows for the creation of smooth surfaces and precise fits, essential for applications like crowns and veneers.
3D Printing: 3D printing also offers a high degree of precision, but it can be more sensitive to resin management, temperature, and parameters, especially in model orientation for slicing. Its ability to create complex geometries makes it suitable for orthodontic devices and complex prostheses, though it may not always match milling's surface smoothness.
Material Usage
Milling: This method involves subtracting material from a solid block, leading to some degree of wastage. Milling can utilize traditional materials with a proven history in dental restorations and can process materials that 3D printing cannot yet handle.
3D Printing: Additive manufacturing is more material-efficient as it builds objects layer by layer, using only the required amount of resin. The range of materials for 3D printing is rapidly expanding and improving in quality, with some restorations now being more commonly produced through printing than milling.
Cost-Effectiveness
Milling: The initial investment in milling equipment can be high, and the cost per restoration can be greater due to material wastage and the need for specialized milling blocks. However, the durability and quality of milled restorations can justify the cost in many cases.
3D Printing: Typically, 3D printing offers a more cost-effective solution, especially for practices that produce a high volume of restorations. The lower cost of materials and the ability to produce multiple restorations simultaneously can lead to significant savings.
Time Efficiency
Milling: Milling machines can produce restorations relatively quickly, often within an hour, making it suitable for same-day dentistry applications. However, the time can vary depending on the complexity and material.
3D Printing: 3D printing can be time-efficient for batch production, where multiple pieces are printed simultaneously. However, individual restoration printing can be slower than milling.
Suitability for Different Dental Applications
Milling: Best suited for applications where precision and material properties are paramount. Ideal for single-tooth restorations like crowns, inlays, onlays, and veneers. Milling is preferable for long-span bridges and implants due to its ability to use high-strength materials.
3D Printing: Excelling in the production of complex and customizable shapes, 3D printing is ideal for orthodontic appliances, surgical guides, and full-arch dental models. It is invaluable for treatment planning and patient education, quickly producing prototypes and models.
In conclusion, both milling and 3D printing play transformative roles in digital dentistry. Each technology has its strengths and ideal applications. The choice between milling and 3D printing depends on the specific requirements of the dental restoration, including precision, material properties, cost, and production time. As digital dentistry continues to evolve, these technologies complement each other, offering a comprehensive approach to modern dental fabrication.
Case Studies and Research Findings: Wear Resistance of Milled vs. 3D Printed Dental Materials
The evolution of dental materials and fabrication methods has been a subject of extensive research, particularly focusing on the wear resistance of milled and 3D printed materials. This aspect is crucial, as the longevity and performance of dental restorations are directly impacted by their resistance to wear.
Summary of Key Studies
One notable study investigated the wear resistance of 3D printed denture teeth compared to traditional, prefabricated ones. The 3D printed specimens, created using a methacrylate-based photopolymerizing resin and stereolithography (SLA), showed significantly less wear than the prefabricated teeth. Specifically, these 3D printed teeth demonstrated 2 to 3.5 times less wear than other tested materials, indicating a higher resistance to occlusal forces and abrasion. This is attributed to the uniform and homogenous structure of the 3D printed material, as opposed to the layered composition of conventional denture teeth.
In contrast, milled dental materials, especially those made from ceramics and high-strength resins, are known for their durability and wear resistance. However, the research comparing the wear resistance of milled materials to 3D printed ones is still emerging. Preliminary findings suggest that while milled restorations exhibit excellent wear resistance, the newer 3D printed materials are rapidly closing the gap, thanks to advancements in resin technology and printing processes.
Clinical Implications
The findings of these studies have significant clinical implications:
Durability of Restorations: The superior wear resistance of 3D printed denture teeth indicates a potential for longer-lasting restorations. This could lead to reduced frequency of replacement, offering cost savings and convenience for patients.
Material Selection: The results support the notion that material selection should be based on the specific application and wear requirements. For instance, 3D printed materials could be more suitable for dentures, while milled ceramics might be preferred for crowns and bridges where esthetics and strength are critical.
Customization and Patient Comfort: The ability to create durable, custom-fit 3D printed prostheses could enhance patient comfort and satisfaction. This is particularly relevant for dentures, where fit and wear are key to functionality and comfort.
Long-Term Performance: Understanding the wear characteristics of different materials helps in predicting the long-term performance of restorations. It assists dentists in making informed decisions about the most suitable materials for their patients, considering factors like the patient's bite force and dietary habits.
Advancements in Dental Fabrication Technologies: The ongoing research highlights the rapid advancements in dental fabrication technologies. As 3D printing technology continues to evolve, it could offer more durable and wear-resistant materials, further broadening its applications in dentistry.
In summary, the research comparing the wear resistance of milled and 3D printed dental materials provides valuable insights into the performance and durability of these restorations. As technology advances, these findings will guide material selection and fabrication methods, ultimately leading to improved patient outcomes and satisfaction in dental care.
Future Trends and Predictions in Dental Fabrication
The landscape of dental fabrication is poised for profound transformations, driven by relentless innovation and technological advancements. As we look to the future, several emerging trends are set to redefine the standards of care and efficiency in digital dentistry.
Integration of AI and Machine Learning
Artificial Intelligence (AI) and machine learning are set to play a pivotal role in dental fabrication. These technologies will enhance the capabilities of CAD/CAM software, enabling more precise and personalized dental restoration designs. AI algorithms could predict optimal restoration shapes and materials based on patient-specific data, leading to better fitting and more durable prostheses.
Advanced Materials
The development of new materials for both milling and 3D printing will continue to expand the possibilities in dental fabrication. These materials will not only offer superior wear resistance and aesthetic qualities but also possess biocompatible and bioactive properties, promoting better integration with the patient's natural tissues.
Augmented Reality and Virtual Reality
Augmented Reality (AR) and Virtual Reality (VR) technologies are expected to revolutionize patient consultation and treatment planning. Dentists could use these tools to visualize and simulate the final outcome of a dental restoration, enhancing patient understanding and involvement in their treatment.
Sustainability in Dental Fabrication
Sustainability will become a key consideration in dental fabrication. This will involve the development of eco-friendly materials and processes, reducing waste and energy consumption in dental labs, and promoting recycling in dental material manufacturing.
Automated and Robotic Systems
Automation and robotics will further streamline the fabrication process, reducing turnaround times and enhancing precision. Robotic systems could undertake tasks with a high degree of accuracy, ensuring consistent quality across all dental restorations.
In conclusion, the future of dental fabrication is bright with the promise of innovation. These advancements will not only elevate the level of dental care but also enhance patient experiences, making dental treatments more efficient, personalized, and sustainable. As these technologies mature, they will undoubtedly become integral components of digital dentistry, shaping the future of dental health and aesthetics.
Conclusion
The exploration of milling and 3D printing technologies in dental fabrication reveals a landscape rich in innovation and potential. From the precision and versatility of milling to the customization and material efficiency of 3D printing, these technologies have significantly advanced the field of digital dentistry.
Milling, with its high precision and ability to work with a variety of materials, remains a cornerstone in dental fabrication, particularly for applications requiring detailed accuracy and strength. On the other hand, 3D printing, especially through advancements in stereolithography, has introduced unprecedented levels of customization and complexity in dental prostheses, making it ideal for a wide range of applications from orthodontics to implantology.
The comparative analysis of these two methods highlights their unique advantages and suitability for different dental applications, emphasizing the importance of choosing the right technology based on specific clinical needs. The research on wear resistance further underscores the rapid advancements in material sciences, demonstrating how these technologies are continually improving in terms of durability and performance.
Looking ahead, the future trends in dental fabrication technology, including the integration of AI, the development of new materials, and the adoption of AR/VR technologies, promise to further revolutionize dental care. These innovations are poised to enhance patient experiences, improve treatment outcomes, and make dental care more accessible and sustainable.
In conclusion, the impact of milling and 3D printing technologies on the future of dental care is profound. As these technologies continue to evolve and integrate with other digital advancements, they will not only redefine the standards of dental treatment but also open new horizons for patient care and clinical excellence in the field of dentistry.
Discover the Future with Metadac FZE
Embark on a journey into the future of digital dentistry with Metadac FZE. Whether you're a dental professional seeking to elevate your practice , Metadac FZE is your partner in this transformative journey. Don't miss the opportunity to experience the cutting-edge of dental technology. Contact us today to learn more about our services and how we can help you step into the future of dental excellence with Metadac FZE.
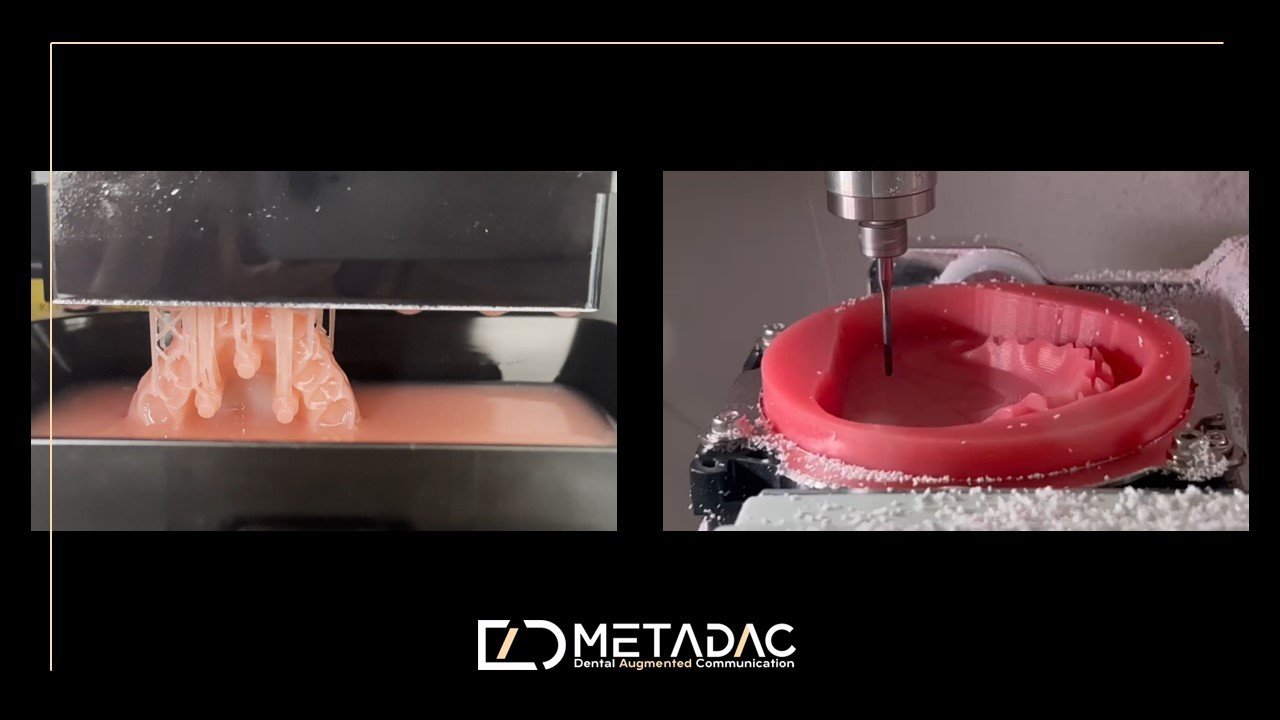
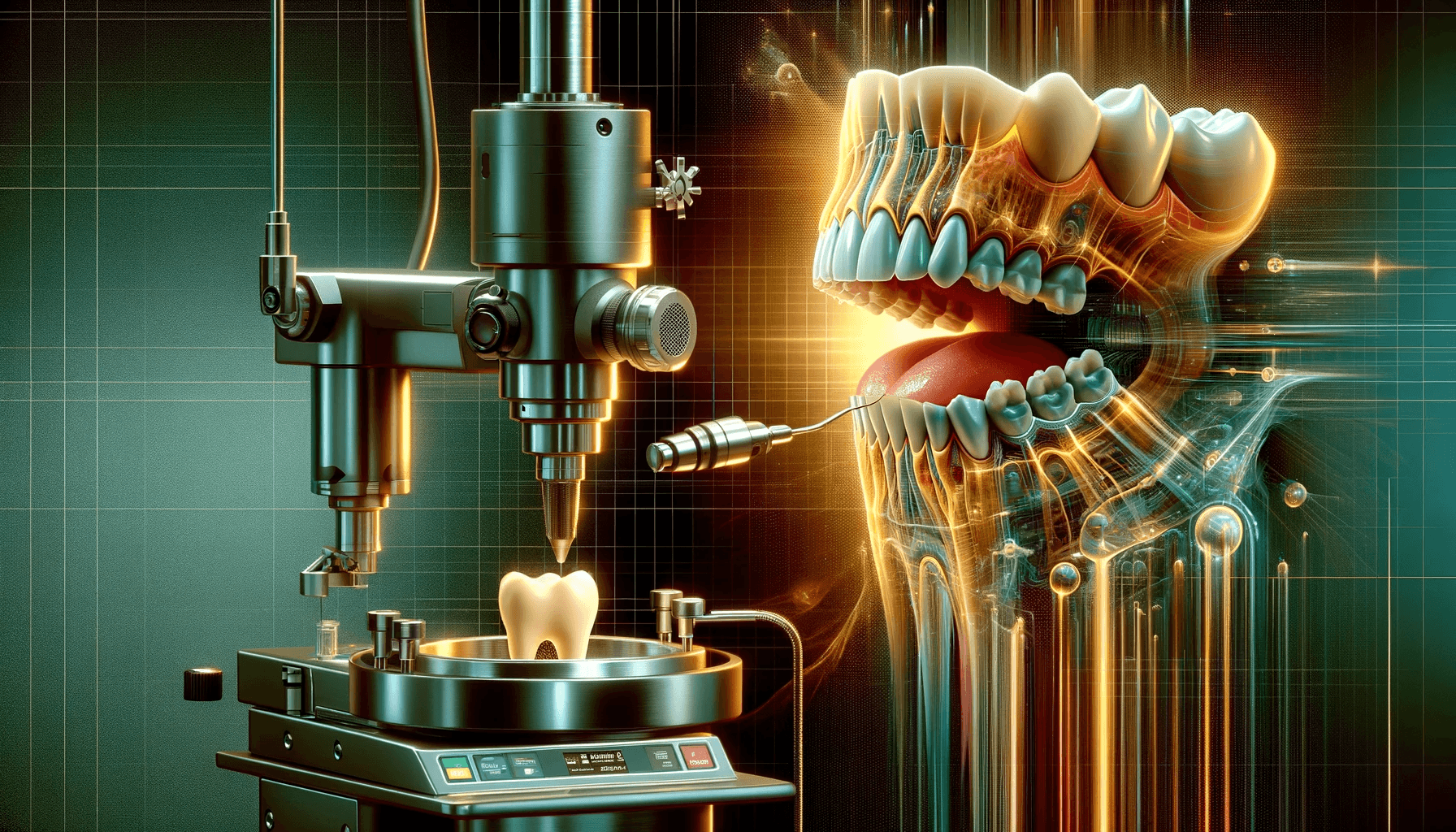