Precision vs Tolerance in Digital Dentistry: Navigating the Analog and Digital Divide
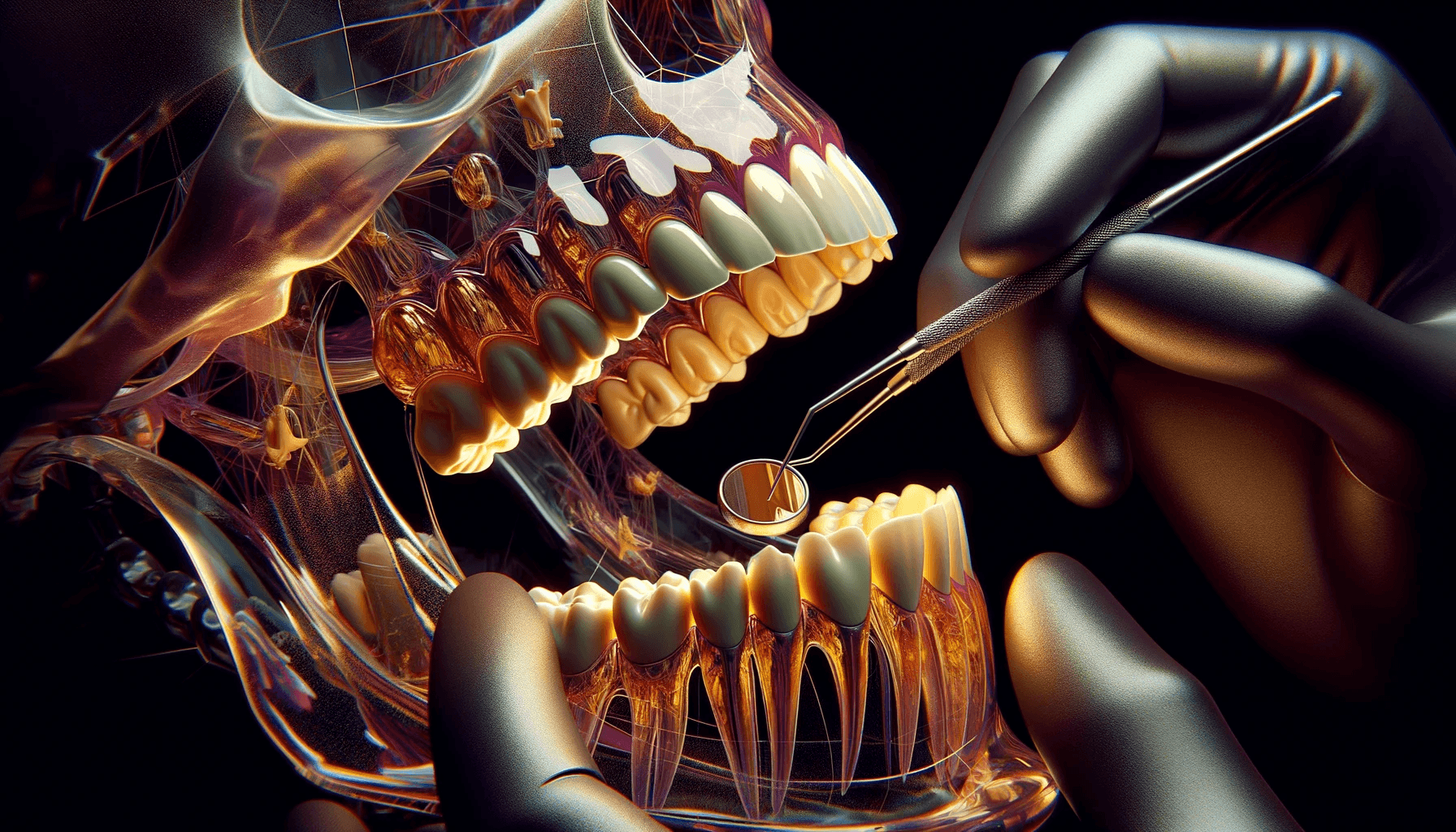
DESCRIPTION
Explore the precision and tolerance in digital dentistry and how it compares to analog methods. Delve into the future of dental accuracy and innovation.
CATEGORY
Milling
CONTRIBUTOR
Alessio Berardi
DATE
03/01/2024
In the realm of dental manufacturing, the pursuit of 'precision' and 'tolerance' stands at the forefront, dictating the success and efficacy of dental treatments and prosthetics. The transition from traditional, analog methods to advanced digital techniques has sparked a significant debate in the dentistry community. While analog approaches have their roots in time-honored craftsmanship, the digital revolution introduces a new paradigm of accuracy and repeatability. This dichotomy raises critical questions: How does the precision of digital methods compare to the artisanal precision of analog techniques? And, does the concept of tolerance - the permissible limit of variation in a physical dimension - differ substantially between these two approaches? As we navigate through the analog versus digital discourse, it becomes imperative to understand and appreciate the nuances of each method in shaping the future of dental manufacturing.
The Digital Revolution in Dentistry
The advent of digital technology in dentistry and precision mechanics has been nothing short of revolutionary. In sectors where millimetric accuracy is not just desired but essential, the digital approach has redefined the standards of precision and efficiency. Digital dentistry, leveraging cutting-edge tools and software, offers unparalleled accuracy in diagnosis, treatment planning, and the creation of dental prosthetics. This precision is particularly pivotal for dental technicians who are now equipped to deliver results with greater consistency and predictability.
A key aspect of this digital transformation is the concept of tolerances in manufacturing processes. Tolerance refers to the permissible deviation from a specified dimension, which is inevitable in any manufacturing process. In the context of dental technology, tolerance dictates the degree of variation allowed in the size and fit of dental appliances or prosthetics. Unlike traditional methods where tolerances were largely dependent on the skill and experience of the technician, digital processes standardize these variations, thereby minimizing human error. This standardization ensures that every manufactured component meets stringent quality criteria, enhancing the overall reliability and effectiveness of dental treatments.
The impact of digital technology, therefore, extends beyond mere precision; it introduces a new level of consistency and reproducibility in dental procedures, fundamentally transforming the dynamics between dental professionals and their craft.
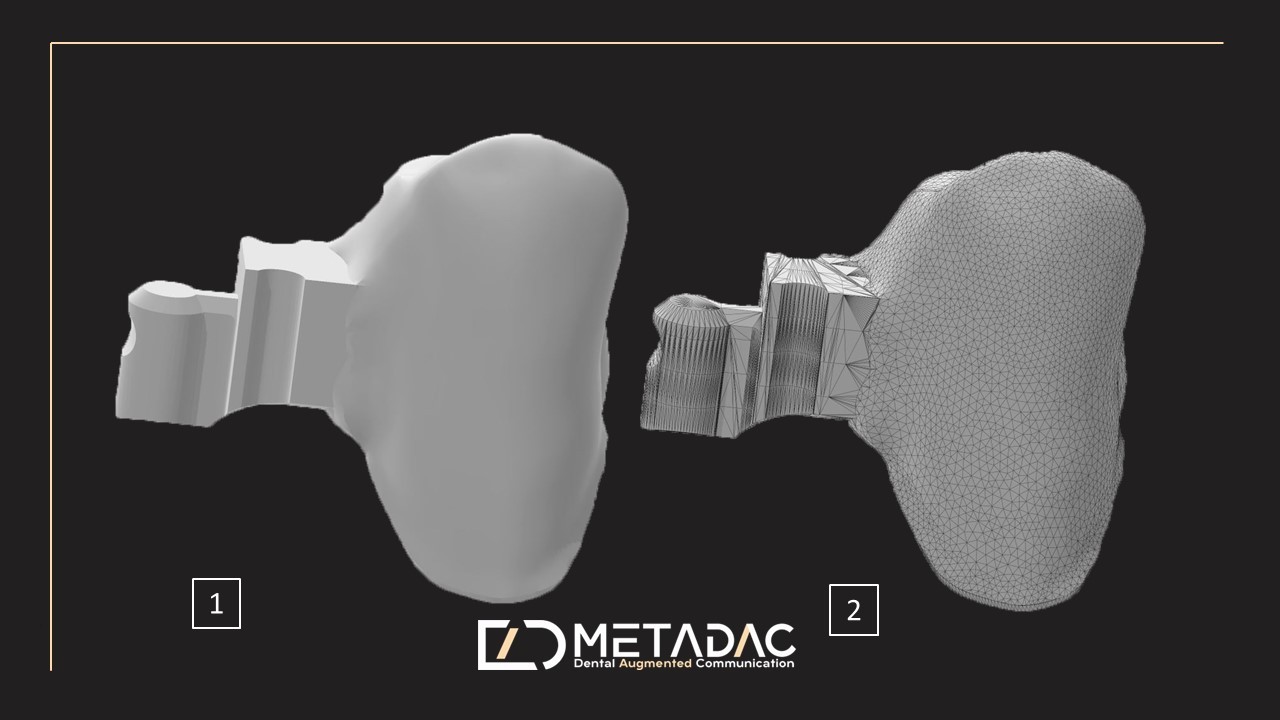
The Heart of Digital: Algorithms and Data Processing
At the core of digital dentistry lies the sophisticated interplay of algorithms, software, and data processing, transforming abstract digital data into tangible dental objects. This process begins with the acquisition of precise measurements or scans of a patient's dental structure. These measurements, represented as a series of coordinates in the Cartesian plane (X-Y-Z), form the foundational data set.
The pivotal role of algorithms comes into play as they interpret this raw data. Sophisticated software algorithms analyze these coordinates, effectively translating numerical values into a comprehensive digital model. This model is a detailed representation of the patient's dental anatomy, constructed through a process called mesh generation. A mesh is a complex network of interconnected points (vertices) forming triangular surfaces, which together create a 3D model of the dental structure. This mesh is not just a static image; it's a dynamic blueprint that guides the subsequent manufacturing processes.
The real magic happens when this digital mesh is transformed into a physical object. Using advanced fabrication technologies like 3D printing or CNC milling, the digital model is brought to life. The software guides these machines, instructing them to replicate the mesh model with extreme precision, layer by layer or through subtractive processes. The accuracy of this transformation from digital to physical is paramount, as it directly influences the fit and functionality of the final dental product.
In essence, the algorithm is the digital craftsman of the modern dental world. Its ability to accurately interpret and transform data into precise physical objects is what sets digital dentistry apart, offering a new horizon of possibilities in dental care and prosthetics.
Precision in Geometric Shapes vs Dental Scans
The comparison between geometric shapes and dental scans in terms of tolerance levels reveals striking differences in how precision is achieved and maintained. In geometric shapes, the concept of 'vertex' and 'surface' plays a crucial role. Simple geometric forms, such as cubes or spheres, have well-defined vertices and surfaces, allowing for lower tolerance levels. This means that the deviation from the intended dimensions can be minimized, as seen in Photos 1 and 2. The regularity and predictability of these shapes enable a more straightforward and precise replication process.
In contrast, dental scans present a unique challenge due to the inherent anatomical irregularities of the human mouth. Unlike the uniformity of geometric shapes, dental structures are complex and vary significantly from person to person. This complexity is evident in the point cloud data generated during a dental scan, where a multitude of points (vertices) are captured to represent the contours and surfaces of teeth and gums. The tolerance levels in dental scans, therefore, need to be more adaptable to accommodate these irregularities.
Photos 3 shows the initial digital representations of these scans, where the surfaces appear reasonably accurate at a macro level. However, upon closer inspection, as in Photos 4, minor discrepancies become apparent. These discrepancies are a direct result of the scanner's ability to interpret the varying topography of dental surfaces. In essence, while geometric shapes allow for minimal tolerance due to their regularity, dental scans require a nuanced approach to tolerance, balancing the need for precision with the reality of anatomical variability. This distinction underscores the complexity and sophistication required in digital dentistry, where precision must be tailored to each unique dental structure.
The Role of Tolerance in CAD Design
In the domain of Computer-Aided Design (CAD) for dental manufacturing, the incorporation of tolerance is a critical factor that significantly impacts the final product's quality and fit. Tolerance in CAD design refers to the allowable variation in dimensions - a 'tolerance gap' - that ensures the manufactured part will function correctly within the intended dental application. This gap accounts for the minute discrepancies that might arise during the manufacturing process, ensuring that the end product aligns precisely with the digital design.
In dental CAD, every micrometer matters. A well-calibrated tolerance gap is essential for ensuring that dental prosthetics, such as crowns or bridges, fit comfortably and accurately in a patient's mouth. For instance, Photo 5 illustrates a section of a CAD design where the software's discharge value is set at 0.00mm. However, upon closer inspection and measurement, the software automatically applies a default tolerance of 0.003mm. This small but significant tolerance accommodates for potential variances in material behavior and machine precision during the fabrication process.
Photo 6 further elucidates this concept, showcasing a design with a software discharge value of 0.035mm. Here, the applied software tolerance brings the actual value to 0.041mm. Such adjustments, though seemingly minor, are pivotal in ensuring that the finished dental piece will fit precisely as intended, without being too tight or loose.
The importance of accurately calibrating these tolerances cannot be overstated. Incorrect tolerances can lead to ill-fitting dental appliances, causing discomfort or even clinical complications for patients. Therefore, dental technicians and CAD designers must possess a deep understanding of both the material properties they are working with and the capabilities of their manufacturing equipment. This knowledge allows them to set tolerances that strike the perfect balance between tight fit and manufacturability, ensuring the highest standards of quality and patient satisfaction.
In summary, tolerance in CAD design is a fine art that blends scientific precision with practical application. It demands a meticulous approach to ensure that the digital design translates into a tangible product that meets the exacting standards of modern dental care.
CAM Processes and Tolerance Values
Computer-Aided Manufacturing (CAM) in dental technology is an intricate process where the translation of digital designs into physical objects occurs. This process heavily relies on the concept of fabrication tolerance, a critical factor determining the precision and quality of the final dental product. CAM systems use digital files, often in the STL format, as blueprints to fabricate dental prosthetics or components through subtractive (milling) or additive (3D printing) methods.
Fabrication tolerance in CAM is the permissible degree of variation from the digital design during the manufacturing phase. This tolerance is essential to compensate for the minute inconsistencies inherent in any fabrication process, whether due to material characteristics or the limitations of the manufacturing equipment. For instance, regarding a rough grinding operation, the initial step in material removal, the tolerance of 0.05 mm is applied. This initial stage prepares the material for more detailed work, allowing for the removal of excess material while leaving room for finer details to be added later.
The contrasts is with a finishing operation, where a much tighter tolerance of 0.01 mm is used. This stage is crucial for defining the final appearance and precision fit of the dental product, ensuring it matches the original design specifications closely. The difference in tolerance values between rough grinding and finishing stages underlines the importance of adjusting these values according to the specific stage of the manufacturing process.
The distinction between mechanical STL files and customized dental files is another key aspect of CAM in dentistry. Mechanical STL files, typically used in engineering and industrial contexts, often represent objects with standardized, geometric shapes. In contrast, customized dental STL files represent complex, patient-specific anatomical structures requiring a higher level of precision. Dental files must account for unique contours and variations of individual patients' oral anatomy, necessitating more refined and accurate fabrication tolerances.
In essence, CAM processes in dental technology are a delicate balance between the digital precision of CAD designs and the physical realities of material and machine capabilities. The judicious application of fabrication tolerances at different stages of the manufacturing process ensures that the final dental products not only meet the aesthetic and functional requirements but also conform to the unique anatomical needs of individual patients.
Conclusion: Precision in Analog vs Digital Dentistry
The exploration of precision and tolerance in the realms of analog and digital dentistry reveals a nuanced landscape. Digital dentistry, with its reliance on algorithms, CAD/CAM processes, and sophisticated data analysis, offers a level of precision measured in microns that was previously unattainable with analog methods. The digital approach provides 'certain data' - precise, measurable, and replicable - ensuring consistency and predictability in dental manufacturing.
In contrast, analog techniques, while rich in craftsmanship and experience, lack this exactitude. The subjective nature of human skill and judgment in analog methods introduces variability that is inherently less precise than the digital approach. Digital dentistry's ability to precisely measure and control every aspect of the manufacturing process, from initial scans to the final product, underscores its superiority in terms of precision.
In conclusion, while analog methods have their merits, it is clear that digital dentistry stands out in its ability to achieve and maintain a higher level of precision. This precision is not just theoretical but is practically significant, impacting the quality of dental care and patient outcomes.

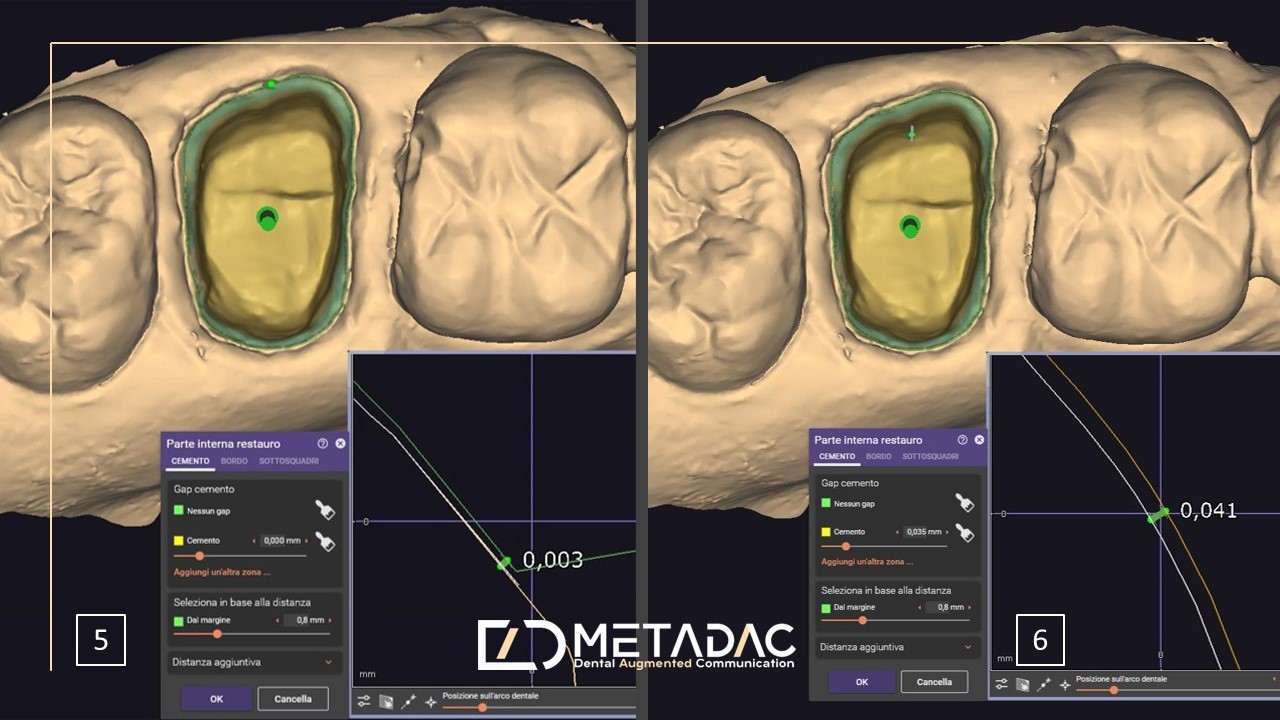